In 2018, the FMCSA issued 185,592 violations to companies for not having properly adjusted brakes (393.47E Brakes (All Others) – Clamp or Roto Type Brake Out of Adjustment). Not only is this an extremely dangerous problem to have, but it’s also avoidable with a little background on the different components that make up an air braking system and a solid fleet maintenance program in place to identify problems before they occur.
Brief Overview
An air compressor mounted to the engine block fills the air tanks up to around 90-105 psi. Air is routed to the push/pull valves in the cab which are used to apply or release the brakes. When the valves are pulled out, the air is cut off and the brakes automatically push against the drums (given the proper brake shoe adjustment). When the valves are pressed in, the air flows through the brake lines to the brake chambers which releases the outward spring pressure. The Brake Chamber push-rod attaches to a Slack Adjuster and the slack adjuster turns an S-Cam that applies pressure directly to the brake shoes.
Here’s what the air system looks like on the power unit:
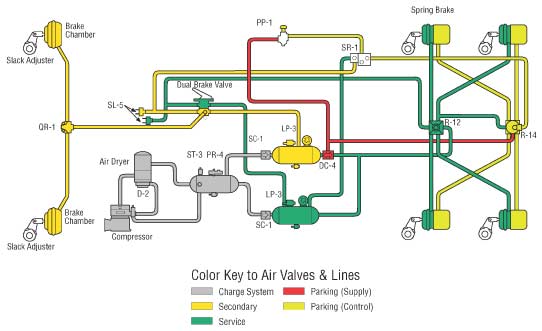
The FMCSA takes brake safety very seriously. With all the coverage from the Colorado incident, it is likely that even more emphasis will be placed on driver training and inspection processes. Whether we like it or not, drivers and companies are going to have to invest in proper brake inspection programs as well as training procedures in the event of brake overheating or air-system failure.
Section 393.47 in the FMCSA rule books says:
(a) General requirements. Brake components must be constructed, installed and maintained to prevent excessive fading and grabbing. The means of attachment and physical characteristics must provide for safe and reliable stopping of the commercial motor vehicle.
(b) Brake chambers. The service brake chambers and parking brake chambers on each end of an axle must be the same size.
(c) Slack adjusters. The effective length of the slack adjuster on each end of an axle must be the same.
(d) Linings and pads. The thickness of the brake linings or pads shall meet the applicable requirements of this paragraph –
(1) Steering axle brakes. The brake lining/pad thickness on the steering axle of a truck, truck-tractor or bus shall not be less than 4.8 mm (3⁄16 inch) at the shoe center for a shoe with a continuous strip of lining; less than 6.4 mm (1⁄4 inch) at the shoe center for a shoe with two pads; or worn to the wear indicator if the lining is so marked, for air drum brakes.
The steering axle brake lining/pad thickness shall not be less than 3.2 mm (1⁄8 inch) for air disc brakes, or 1.6 mm (1⁄16 inch) or less for hydraulic disc, drum and electric brakes.
(2) Non-steering axle brakes. An air braked commercial motor vehicle shall not be operated with brake lining/pad thickness less than 6.4 mm (1⁄4 inch) or to the wear indicator if the lining is so marked (measured at the shoe center for drum brakes); or less than 3.2 mm (1⁄8 inch) for disc brakes. Hydraulic or electric braked commercial motor vehicles shall not be operated with a lining/pad thickness less than 1.6 mm (1⁄16 inch) (measured at the shoe center) for disc or drum brakes.
In addition to these braking systems, many commercial vehicles are equipped with other safety features such as anti-lock brakes (ABS), traction control, and stability control. These features work to help prevent accidents by providing the driver with more control over the vehicle in challenging driving conditions.
A little knowledge can go a long way in keeping your trucks on the road. Making sure you and your drivers are familiar with the braking systems and adjustment requirements is a small step you can take to keep your trucks in service and eliminate unnecessary citations.
Regular Inspections
Regular inspections of the air brake system are necessary to identify any potential problems early. Inspections should include checking for leaks, worn or damaged components, and proper adjustment of brake linings.
Commercial Vehicle Driver Training
Drivers should receive training on the proper use and maintenance of air brake systems. They should be taught how to recognize signs of brake problems and know what to do in the event of a brake failure. Some key areas to focus the training should include:
- Identifying brake systems that are out of adjustment
- Identifying the signs of stuck/hung brakes
- Proper use of air brake systems
Common Reasons for Air Brake Failures
Truck and trailer braking systems can fail due to various reasons, such as inadequate maintenance, misaligned brake shoes, leaky air lines, overheating, and other mechanical problems. Any issue with the braking system is critical and repair should not be delayed. Furthermore, companies can save on maintenance costs by providing in depth training of the best practices for maximizing brake component lifespan and safety practices like utilizing the self adjustment feature on the slack adjusters from inside the cab of the vehicle.
Air Dryers
An air dryer system on a commercial motor vehicle is a filtration system that removes contaminants and moisture from the compressed air used in the brake system. The air dryer is installed between the compressor and reservoirs and collects solid, liquid, and vapor contaminants before they enter the air brake system. The compressed air is forced through a filtration system filled with desiccant, which removes moisture from the compressed air. Moisture can cause corrosion and other damage to the brake system components, so it is important to maintain the air dryer to ensure proper operation of the brakes.
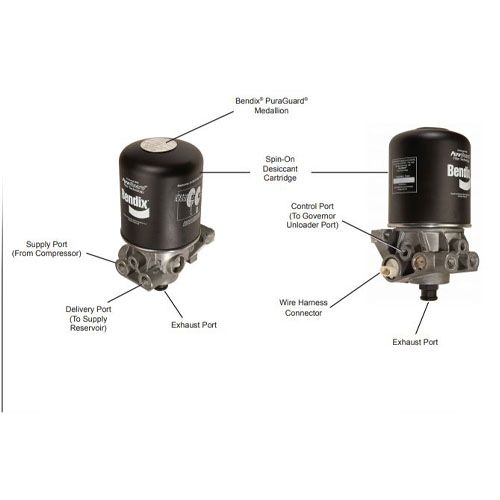
Warning: Extreme caution should be used when working on any part of commercial vehicle braking systems. When pressurized, serious injury and even death can occur from a simple mistake.
